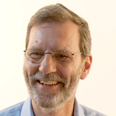
Recently my wife came home from a local sewing shop proudly waving a large piece of material, which turned out to be a “swatch book” for quilting fabrics. She now has it pinned up on the wall of her hobby room.
It made me wonder how many separations or spot colors I’d ever seen in a single job myself … ignoring jobs specifically designed as swatches.
I think my personal experience probably tops out at around 18 colors, which was for a design guide for a fuel company’s forecourts after a major redesign of their branding. It was a bit like a US banknote: lots of colors, but most of them green!
But I do occasionally hear about cases where a print company or converter, especially in packaging, is looking to buy a new digital press. I’m told it’s common for them to impose together all of their most challenging jobs on the grounds that if the new press (or rather, the DFE on the new press) can handle that, then they can be confident that it’ll handle any of the jobs they receive individually. Of course, if you gang together multiple unrelated jobs, each of which uses multiple spot colors, then you can end up with quite a few different ones on the whole sheet.
“Why does this matter?” I hear you ask.
It would be easy to assume that a request for a spot color in the incoming PDF file for a job is very ephemeral; that it’s immediately converted into an appropriate set of process colors to emulate that spot on the press. Several years ago, in the time of PostScript, and for PDF prior to version 1.4, you could do that. But the advent of live transparency in PDF made things a bit harder. If you naïvely transform spots to process builds as soon as you see them, and if the spot colored object is involved in any transparency blending, then you’ll get a result that looks very different to the same job being printed on a press that actually has an ink for that spot color. In other words, prints from your digital press might not match a print from a flexo press, which is definitely not a good place to be!
So in practice, the RIP needs to retain the spot as a spot until all of the transparency blending and composition has been done, and can only merge it into the process separations afterwards. And that goes for all of the spots in the job, however many of them there are.
Although I was a bit dismissive of swatches above, those are also important. Who would want to buy a wide format printer, or a printer for textiles, or even for packaging or labels, if you can’t provide swatches to your customers and to their designers?
All of this really came into focus for me because, until recently, the Harlequin RIP could only manage 250 spots per page. That sounds a lot, but wasn’t enough for some of our customers. In response to their requests we’ve just delivered a new revision to our OEM partners that can handle a little over 8000 spots per page. I’m hoping that will be enough for a while!
If you decide to take that as a challenge, I’d love to see what you print with it!