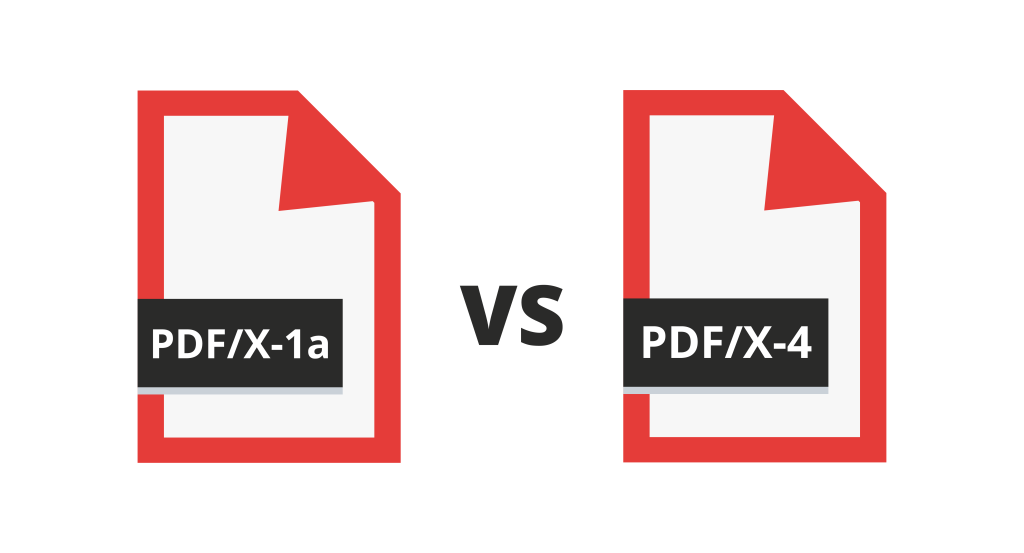
We’ve noticed more customers asking about PDF/X-1a lately, especially how it compares to PDF/X-4. While both are PDF standards designed for reliable print production, they serve slightly different purposes, and it’s worth knowing how their relevance has changed over time.
Quick Overview
Both PDF/X-1a and PDF/X-4 are ISO standards built to ensure predictable, press-ready PDF files. They limit certain PDF features to avoid issues at the RIP (Raster Image Processor) and ensure consistency in professional printing environments.
But each handles color, transparency, and workflow flexibility differently:
PDF/X-1a (2001)
- Color requirements: All content must be converted to CMYK or spot colors before it’s saved
- No transparency: Any live transparency must be flattened
- All fonts must be embedded
- No layers or optional content
- Responsibility: Everything must be finalized at the design stage. What you send is exactly what will be printed
Why it was popular
In the early days of PDF-based print workflows, it was all too easy for a job to fail, due to the lack of the correct font, unpredictable color conversion and much more. PDF/X-1a solved many of these problems, making PDF a reliable container for sending print jobs to print. It continued to be popular after PDF 1.4 was introduced, which added transparency to PDF, because RIPs varied in how well they handled transparency and color management. Flattening and converting everything to CMYK upfront made print outcomes more predictable—especially when working with older RIPs or less color-savvy printers.
When might PDF/X-1a still be useful?
Despite being over a quarter of a century old, PDF/X-1a hasn’t gone away; it is still used in workflows where reliability is valued over possible disadvantages such as larger file sizes or device-dependence. For example:
- If you’re working with legacy RIPs or printers with rigid workflows.
- If a print service provider explicitly requires flattened, CMYK-only files.
- In regulated industries or environments where absolute predictability is prioritized over flexibility.
PDF/X-4 (2010)
- Supports device-independent color spaces (e.g., RGB, Lab)
- Keeps live transparency
- Supports layers (optional content groups)
- Responsibility: Puts more trust in modern RIPs to handle color separation and transparency rendering at output time.
Why it’s now preferred
Modern workflows, especially with digital presses, rely on advanced RIPs that handle transparency and ICC-based color reliably. PDF/X-4 offers flexibility, forward-compatibility, and easier repurposing across platforms (print, web, mobile).
Why PDF/X-4 is often the better choice today
As of 2025, most production environments—whether offset, digital, inkjet, or flexo—have no problem processing live transparency or color-managed workflows. This means:
- PDF/X-4 allows richer, more flexible files without requiring flattening or color conversion at design time.
- It’s easier to repurpose files across different presses or output methods.
- It supports modern design tools and effects without workarounds.
- It also plays better with hybrid workflows that combine print and digital delivery.
Preflight
Emerging as PDF was adopted for print workflows, software to carry out a “pre-flight” check of PDFs destined for print emerged as a new software category, and PDF/X provided standards that a PDF could be measured against. Rejecting a job before it hits the press can avoid a costly mistake. Moreover, such checks can be automated, and in some cases automatically rectify errors to make the job compliant with the appropriate PDF/X standard.
Final thoughts
The choice between PDF/X-1a and PDF/X-4 is less about technical limitations now and more about workflow preferences and compatibility. For most users and most modern print workflows, PDF/X-4 is the smarter, more future-proof option.
If your print provider still asks for PDF/X-1a, it may be worth asking why—and whether their systems have been updated to support more current standards.
Read more about standards and compliancy on our Mako Core™ web page.
About the author
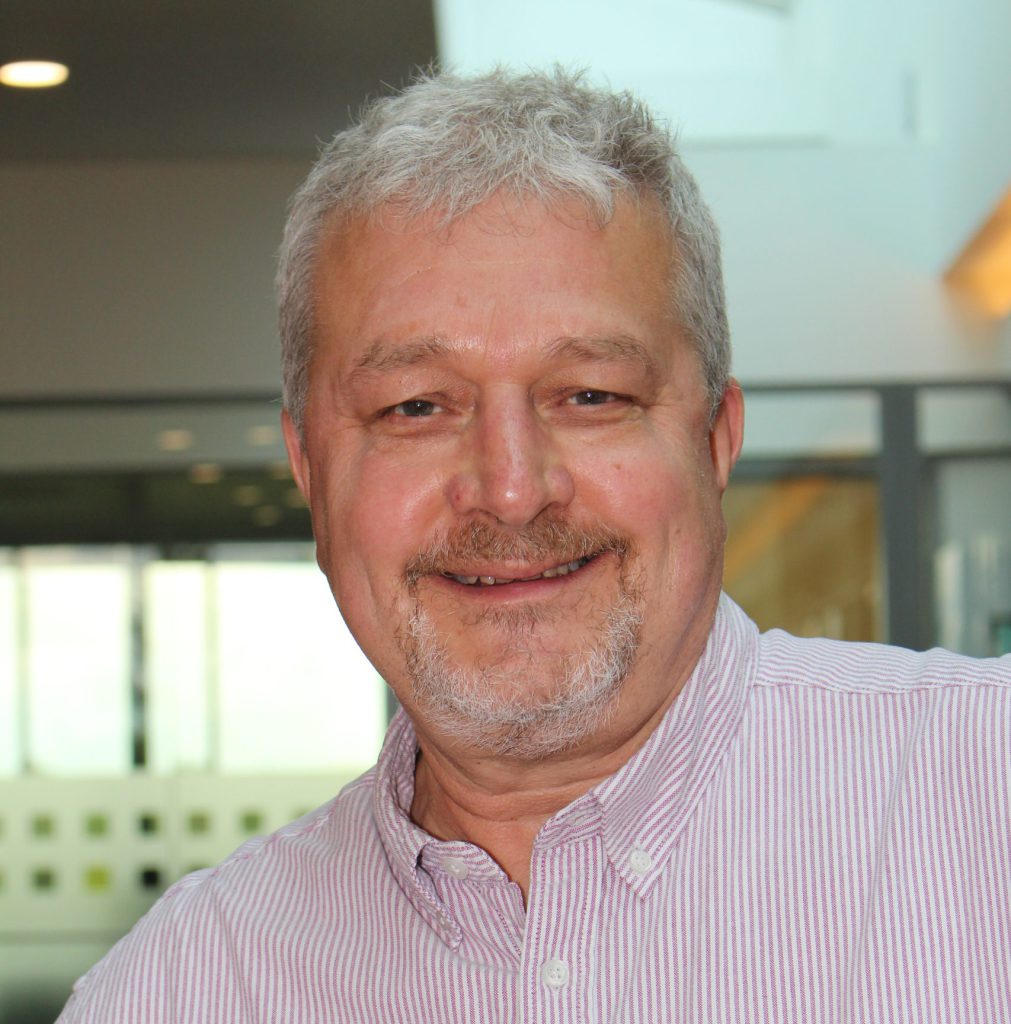
Further reading:
- Compliance, compatibility, and why some tools are more forgiving of bad PDFs
- Film: Choosing a print software development kit (SDK)
Be the first to receive our software release updates, blog posts, company and product news. Why not subscribe to our newsletter? Subscribe