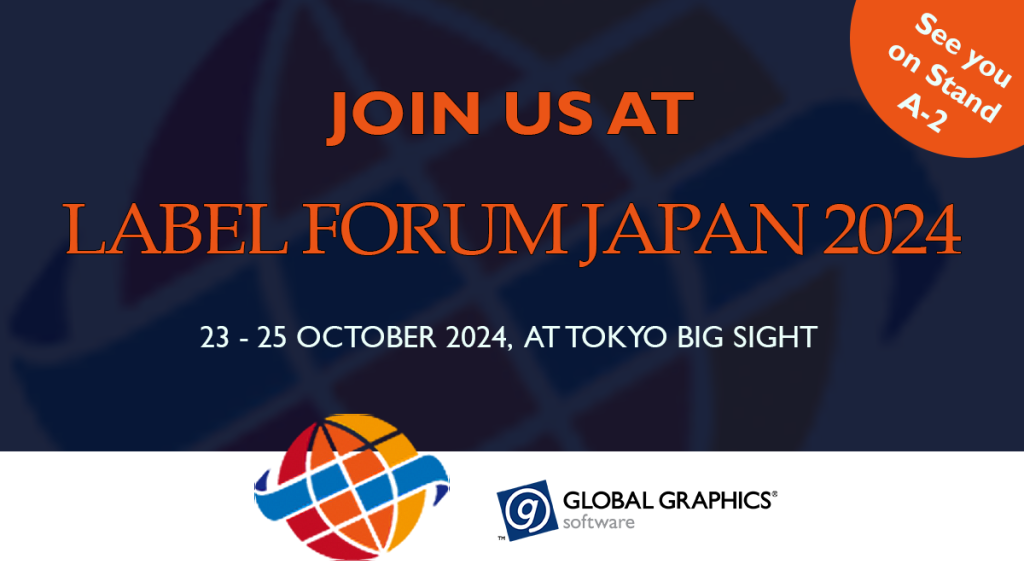
We’re counting down to the Label Forum Japan 2024 in Tokyo (23-25 October 2024), where we’ll be showcasing our latest innovations for print on stand A-2! We hope you can join us. Hagiwara Yoshiyuki-San, our sales director in Japan, is looking forward to welcoming you. Don’t hesitate to contact him to book a meeting at the show.
Here’s what you can expect:
⭐ SmartDFE for Labels and Packaging – The ONLY AI-accelerated, inline Digital Front End for high-speed, single-pass inkjet presses. Discover how easily you can create a custom GUI with OPC UA connectivity.
⭐ SmartDFE for Industrial – Easily add a print subsystem to a smart factory/manufacturing line.
⭐ STEPZ from HYBRID Software – A powerful PDF editor based on the award-winning PACKZ technology, designed for variable data, step & repeat, print optimizations, quality control, and much more.
For more information visit: www.labelforum.jp and contact us to book your personal demo.
Global Graphics Software is part of Hybrid Software, a full-stack software and electronics supplier at the heart of industrial inkjet printing. With 100% IP ownership, we continuously innovate and improve our solutions without third-party limitations. Independent from any printer manufacturer, our solutions are designed with your success in mind. Our flexible software components empower your engineers to tailor solutions to your specific needs, giving you complete control to make your Digital Front End uniquely yours.
Be the first to receive our blog posts, news updates and product news. Why not subscribe to our monthly newsletter? Subscribe here