A few years ago, Global Graphics Software partnered with ink delivery system builder APS Engineering to develop a groundbreaking solution: the first OPC UA-enabled ink delivery system (IDS). OPC UA is the interoperability standard for exchanging data securely and reliably in the industrial automation space. It ensures the seamless flow of information among devices, regardless of the manufacturer or platform.
Initially a prototype, the IDS connected to Global Graphics Software’s SmartDFE™, the AI-accelerated Digital Front End for inkjet presses, and could seamlessly communicate with other components in the industrial inkjet ecosystem.
The IDS exposed all control and monitoring parameters to the OPC UA client, enabling remote monitoring and control. Additionally, it allowed the client to extract key information on consumables, such as fluid consumption, facilitating predictive maintenance, a key feature for improving operational efficiency and minimizing downtime in smart factories. The solution proved to be a significant leap forward, showcasing how advanced connectivity and automation can enhance the performance of industrial printing systems.
Building on the prototype success, APS Engineering has now integrated the Arduino OPTA micro PLC1 into its Mega ink delivery system. The Mega is a powerful pumping system, equipped to tackle large-scale production with 700 cc per minute flow rate and capacity to support up to twelve printheads.
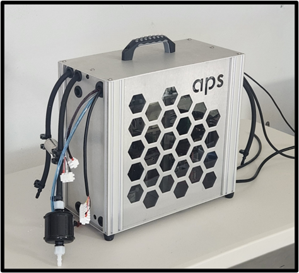
Jaren Marler, CEO of APS Engineering comments: “This integration greater simplifies connectivity and offers a cost-effective, certified solution for both prototyping and full-scale production. Going forward, all our ink pumping systems will use the OPTA micro PLC and will be fully OPC UA-enabled. With the combination of Arduino OPTA and OPC UA, APS Engineering’s ink delivery systems continue to advance, providing enhanced capabilities for our customers.”
Eric Worrall, VP of Products and Services at Global Graphics Software, adds: “It’s fantastic to see another component of an inkjet press adopting a secure-by-design communication standard like OPC UA. This allows us to seamlessly integrate data from the ink delivery system directly into the Smart Print Controller in SmartDFE or connect it to our cloud data services. And because it’s all done securely, we’re well positioned as cybersecurity compliance becomes increasingly embedded in law.”
For more information, read our smart connectivity page.
Check out this demonstration showing how our prototype was used to demonstrate OPC UA connectivity with a Raspberry Pi:
About APS Engineering and the SmartDFE Partner Network
APS Engineering is a member of our SmartDFE Partner Network and a leader in ink delivery systems for inkjet printing, additive manufacturing, and microdispensing.
The SmartDFE Partner Network is a community around SmartDFE, the only AI-accelerated inline Digital Front End for high-speed, single-pass, roll-to-roll inkjet presses. For press manufacturers who are integrating SmartDFE into their own workflows or solutions, they can expand their experience and expertise by calling on one of the SmartDFE partners. The partners have expertise in enhancing connectivity, performance, quality and workflow.
Further reading:
- Streamlining OPC UA integration with Traeger’s SDK
- Developing a customer User Interface for SmartDFE’s Smart Print Controller
- Video: Inkjet printing in smart manufacturing
- Video: How to transform your inkjet business with Industry 4.0 and OPC UA
- Video: Short introduction to the OPC UA
Be the first to receive our software release updates, blog posts, company and product news. Why not subscribe to our newsletter? Subscribe here
1 The Arduino OPTA, developed in partnership with Finder, is a secure, easy-to-use micro PLC with industrial IoT capabilities. It supports both Arduino programming and standard PLC languages, making it versatile for various industrial applications.