Product manager David Stevenson highlights the unrivaled uses of Mako Core™, the Software Development Kit (SDK) at the core of smart print applications
At the end of January, we released Mako Core 7.2.0, the latest of the regular quarterly releases of our very capable SDK for processing PDF and other PDLs such as PCL.
Like most Mako releases, this is a mixture of new development and fixes, almost all inspired by requests from our customers who are putting Mako to work in a wide variety of (mainly print-related) applications.
Its rendering capabilities are on a par with any commercial RIP, and it’s used for everything from generating thumbnails to producing color-correct rasters for driving print devices. We also see it used for interrogating PDFs to see what’s in them – their color spaces, fonts, images etc. Other customers use it for imposition, generating VDP content from templates, visualizing PDFs for print inspections systems, converting to PDF/X standards and much more. SmartDFE™, the smart Digital Front End for high-speed, single-pass digital inkjet presses, also relies heavily on Mako for job editing and many other workflow tasks, including the patented AI-driven job estimation capability.
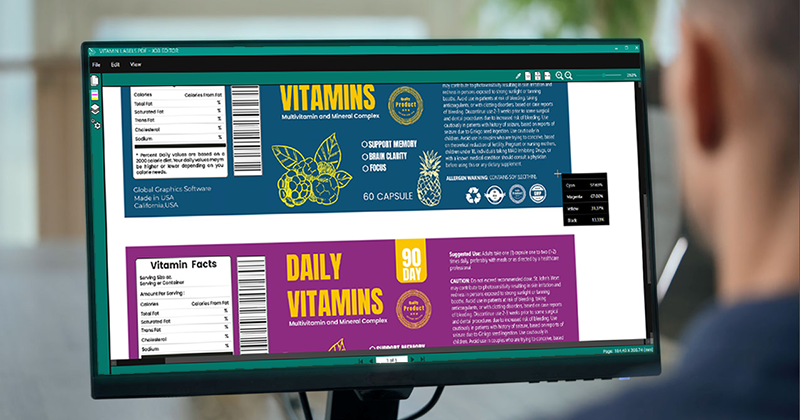
What our customers appreciate (and we know this because they tell us) is our ability to respond quickly to new challenges and that they rarely have to wait long for the solution they need… you can explore some of our success stories in our case studies.
Get in touch if you would like to know more about Mako and how it can help you enhance your print-related applications. For more information contact me via email:
david.stevenson@globalgraphics.com
About the author
David Stevenson is product manager for Mako Core SDK and responsible for the performance component in Global Graphics Software’s SmartDFE, the Digital Front End for high-speed, single-pass inkjet presses.
Be the first to receive our blog posts, news updates and product news. Why not subscribe to our monthly newsletter? Subscribe here