By Tom Mooney, product manager for Global Graphics Software
I’ve just returned from a road trip in the US to inkjet press manufacturers who are all interested in using ScreenPro.
The meetings have gone in a very similar manner with the opening line: “We have a print shop that wants to print this job, but take a look at this area.” They point to an area of the image, usually in the shadows, and it is either a muddy brown mess or crusty and flaky, the typical ‘orange peel’ effect. We all agree the print is unacceptable and cannot be sold, so we discuss what can be done.
Firstly, we look at the ink limitation, but this kills the color saturation in the rest of the print. We look at color management and under color removal, but this only moves the problem to a different area on the image.
Then we see what ScreenPro can do.
We try our Advanced Inkjet Screens™ and use Pearl screen on the muddy mess and Mirror on the orange peel. This does the trick and makes the prints acceptable, so the print shop can sell that print job.
As long as this quality threshold is met the customer is happy. This quality is achieved by a combination of hardware, media and ink and software. Color management is only part of the story with the software – ScreenPro makes a real impact on those hard-to-solve killer jobs.
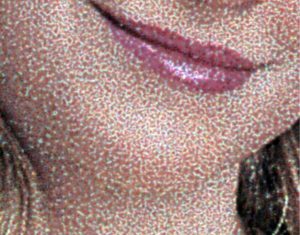