The Inkjet Conference Düsseldorf has been and gone for another year and we’re already looking ahead to the 2019 events that will be organised by ESMA.
This year delegates in the audience were able to submit questions via an app for the first time. I’m grateful to the IJC for sending me the questions that we either didn’t have time to cover after my presentation, or that occurred subsequently. So here they are with my responses:
Is it possible to increase the paper diversity with software by e.g. eliminating paper related mottling?
Yes, we have yet to come across a media/ink combination ScreenPro™ will not work well with. The major artefact we correct for is mottle. This may mean you can print satisfactory results with ScreenPro on papers where the mottle was unacceptable previously, so increasing the diversity of papers that can be used.
It sounds like ScreenPro is very good at tuning a single machine. How do you also then match that output quality among several machines?
There are two technologies in ScreenPro, the screening core itself with the Advanced Inkjet Screens (AIS), and PrintFlat™ to correct for cross web banding. ScreenPro generally improves print quality and Mirror and Pearl screens (AIS) work in the majority of screening situations. PrintFlat, however, needs to be tuned to every press and if the press changes significantly over time, if a head is changed for example, it will have to be recalibrated. This calibration actually makes subsequent ink linearization and colour profiling more consistent between machines as you have removed the cross-web density fluctuations (which are machine specific) from the test charts used to generate these profiles.
“We haven’t found ink or substrate that we couldn’t print with.” Does this include functional materials, such as metals, wood, rubber? or is it limited to cmyk-like processes?
No – with ScreenPro we have only worked with CMYK-like process colours, i.e. print that is designed to be viewed with colour matching etc. ScreenPro is designed to improve image quality and appearance. I see no reason why ScreenPro would not work with functional materials but I would like to understand what problems it is trying to solve.
What is the main innovation of the screening software in terms of how it works as opposed to what it can do?
“How it works” encompasses placing the drops differently on the substrate in order to work around common inkjet artefacts. The innovation is therefore in the algorithms used to generate the screens.
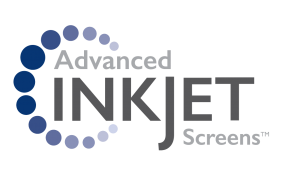