Halftone screening, also sometimes called halftoning, screening or dithering, is a technique to reliably produce optical illusions that fool the eye into seeing tones and colors that are not actually present on the printed matter.
Most printing technologies are not capable of printing a significant number of different levels for any single color. Offset and flexo presses and some inkjet presses can only place ink or no ink. Halftone screening is a method to make it look as if many more levels of gray are visible in the print by laying down ink in some areas and not in others, and using such a small pattern of dots that the individual dots cannot be seen at normal viewing distance.
Conventional screening, for offset and flexo presses, breaks a continuous tone black and white image into a series of dots of varying sizes and places these dots in a rigid grid pattern. Smaller dots give lighter tones and the dot sizes within the grid are increased in size to give progressively darker shades until the dots grow so large that they tile with adjacent dots to form a solid of maximum density (100%). But this approach is mainly because those presses cannot print single pixels or very small groups, and it introduces other challenges, such as moiré between colorants and reduces the amount of detail that can be reproduced.
Most inkjet presses can print even single dots on their own and produce a fairly uniform tone from them. They can therefore use dispersed screens, sometimes called FM or stochastic halftones.
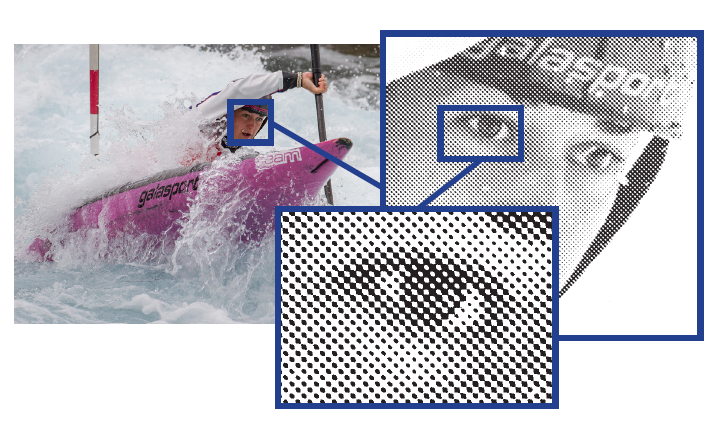
A dispersed screen uses dots that are all (more or less) the same size, but the distance between them is varied to give lighter or darker tones. There is no regular grid placement, in fact the placement is more or less randomized (which is what the word ‘stochastic’ means), but truly random placement leads to a very ‘noisy’ result with uneven tonality, so the placement algorithms are carefully set to avoid this.
Inkjet is being used more and more in labels, packaging, photo finishing and industrial print, all of which often use more than four inks, so the fact that a dispersed screen avoids moiré problems is also very helpful.
Dispersed screening can retain more detail and tonal subtlety than conventional screening can at the same resolution. This makes such screens particularly relevant to single-pass inkjet presses, which tend to have lower resolutions than the imaging methods used on, say, offset lithography. An AM screen at 600 dots per inch (dpi) would be very visible from a reading distance of less than a meter or so, while an FM screen can use dots that are sufficiently small that they produce the optical illusion that there are no dots at all, just smooth tones. Many inkjet presses are now stepping up to 1200dpi, but that’s still lower resolution than a lot of offset and flexo printing.
This blog post has concentrated on binary screening for simplicity. Many inkjet presses can place different amounts of ink at a single location (often described as using different drop sizes or more than one bit per pixel), and therefore require multi-level screening. And inkjet presses often also benefit from halftone patterns that are more structured than FM screens, but that don’t cluster into discrete dots in the same way as AM screens.
The above is an excerpt from our latest white paper: How to mitigate artifacts in high-speed inkjet printing. Download the white paper here.