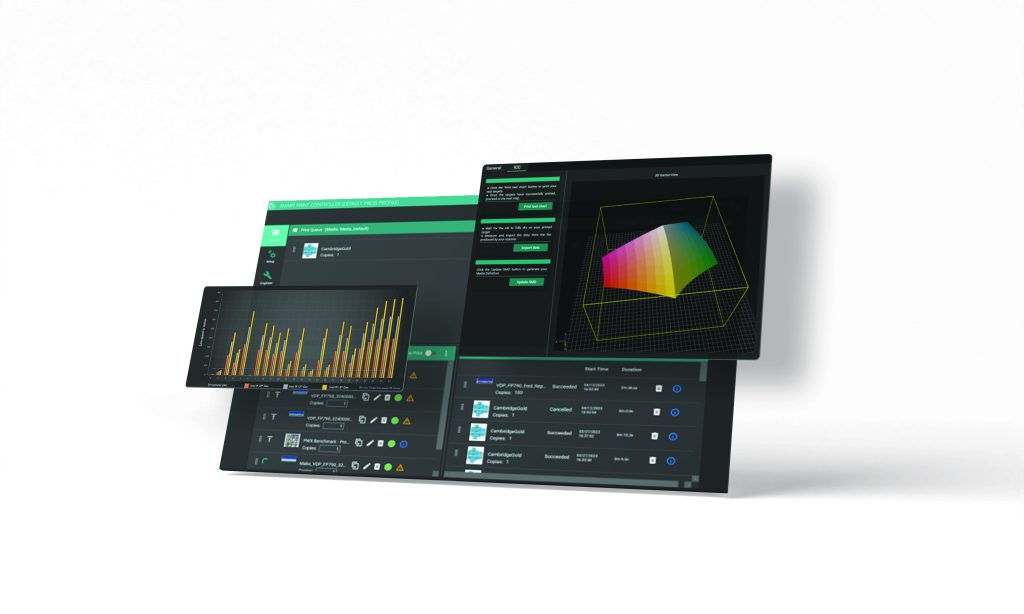
We’re excited to announce the release of SmartDFE™ Version 4.11, now available for download from the FTP site as of early April 2025. This version introduces several powerful enhancements.
This release includes fewer new features than usual because we’re focusing on developing a new SmartDFE component called Label Studio. We look forward to sharing more about Label Studio with you when version 4.12 is released at the beginning of July.
In version 4.11, we’ve made several improvements to the Job Editor. Previously, you could move objects defined by a spot color into the process color space, but doing so would remove the spot color and prevent further editing. Now, you can change a spot color’s representation—from Lab color to device color space—without losing the spot. This means you can edit the spot later, whether you want to adjust the device color or revert to Lab color. Additionally, we now clearly indicate when a spot is out of gamut, has an edited Lab color, or has been converted to the device space.
We have also updated the Smart Media Manager with a fresh look and new icons that better reflect their functions. The previous “project” concept, which dated back to an earlier version of our tools, has been removed. Smart Media Manager now works directly with Smart Media Definitions. This streamlined workflow allows you to retrieve an SMD for the print controller, make edits, and then easily reintegrate it.
Finally, we’ve enhanced the Meteor Router component. The OPC UA interface now provides integrators with greater visibility into the state of Meteor controllers during startup. We have also improved the logging capabilities of the Meteor Router to better support complex installations that involve multiple Meteor controller boards with many heads.
You can see the full list of improvements here: SmartDFE v4.11 Release Notes
About the author
Eric Worrall currently leads the product management and technical services teams as well as being responsible for the product strategy, position and vision within Global Graphics Software. He has had a wide experience of key roles including senior software developer, technical support, sales and product management, and has over twenty years of market knowledge in printing, digital documents, machine vision technologies.
Further reading:
Be the first to receive our software release updates, blog posts, company and product news. Why not subscribe to our newsletter? Subscribe here