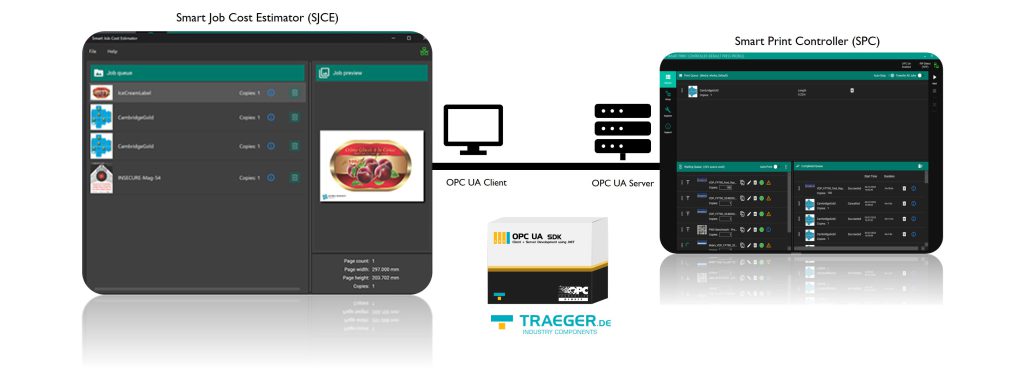
As a supplier of intelligent software components to the industrial print industry, we are fortunate to work with many outstanding, innovative companies – not just customers, but also partners we can collaborate with and learn from. Traeger Industry Components is one such partner. An industrial communications technology company, Traeger is one of the leading providers of solutions for the requirements of Industry 4.0. We first discovered their technology when we integrated secure communication into our SmartDFE™ and we were thrilled when they joined our SmartDFE Partner Network.
SmartDFE is a Digital Front End for single-pass inkjet presses in industrial settings. A key feature is its connectivity and smooth integration with factory control systems. We wanted to use a secure open industry standard to enable this connectivity and chose OPC UA (Open Platform Communications Unified Architecture). Developed by the OPC Foundation, OPC UA is a machine-to-machine communication protocol used for industrial automation.
To ensure smooth integration, particularly with OPC UA clients, we needed to adhere to the OPC UA open standard. OPC UA can give you incredible functionality and control with only a small amount of code, but it can sometimes be daunting for engineers to work with a technology that they are unfamiliar with.
Recognizing this challenge, we turned to Traeger, whose software development kits (SDKs) are specifically designed to simplify the development of OPC UA servers and clients. Using their SDK to integrate OPC UA into our .NET-based applications within SmartDFE not only accelerated our development process but also provided invaluable support.
Thanks to Traeger’s robust SDK, we were able to implement OPC UA communication efficiently, allowing our fully .NET-based SmartDFE to perform optimally. By leveraging Traeger’s expertise, we have significantly reduced the complexity and time associated with adopting OPC UA, enabling us to deliver a more integrated and reliable product to our customers.
This partnership has proven so effective that our customer, Mark Andy Inc, also adopted Traeger’s SDK to integrate the Print Controller of their Digital Series HD high-speed press with our SmartDFE, further validating the strength and utility of Traeger’s solutions.
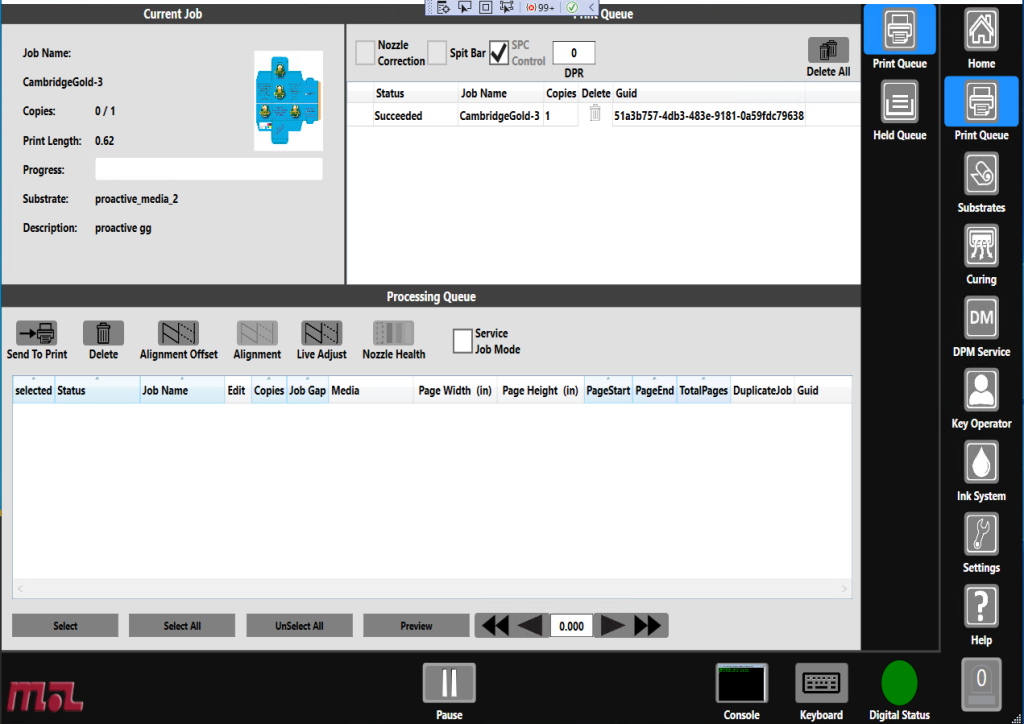
Juliana Cressman, R & D manager at Mark Andy Inc, shares her experience:
“Mark Andy’s latest high-speed digital press is powered by Global Graphics Software’s SmartDFE. It provides a world-class digital printing workflow that enables printing fully variable data at 480 fpm (146 mpm). On Global Graphics Software’s recommendation, we chose the Traeger OPC UA Client SDK to integrate the Smart Print Controller into the press. The Traeger OPC UA Client API was simple to use and well documented. Our team, with minimal knowledge of OPC UA, was able to connect to the OPC UA Server to read and write data reliably. The product works robustly in our system, and the experience with Traeger has been pleasant.”
Dominik Scharnagl, managing director of Traeger comments:
“Our collaboration with Global Graphics is a great example of the powerful capabilities of our OPC UA SDK in action. It’s impressive to see how Global Graphics leverages our technology to create innovative solutions that simplify integration while enhancing efficiency and flexibility. We deeply value the trust placed in us and are excited to work together on projects that make a real technical and economic impact.”
About the SmartDFE Partner Network
The SmartDFE Partner Network is a community around SmartDFE™, the only AI-accelerated inline Digital Front End for high-speed, single-pass, roll-to-roll inkjet presses.
For press manufacturers who are integrating SmartDFE into their own workflows or solutions, they can expand their experience and expertise by calling on one of the SmartDFE partners. The partners have expertise in enhancing connectivity, performance, quality and workflow.
Further reading:
- Blog post: Developing a custom User Interface for SmartDFE’s Print Controller
- Video: Inkjet printing in smart manufacturing
- Video: How to transform your inkjet business with Industry 4.0 and OPC UA
- Video: Short introduction to the OPC UA
Be the first to receive our software release updates, blog posts, company and product news. Why not subscribe to our newsletter? Subscribe here