Our latest case study highlights Jetron Digital Printing Systems, a leading developer of digital printing technologies in industrial printing processes. They were looking for a high-performance Raster Image Processor (RIP) that could efficiently handle complex graphics and large files for their D2 Shape and D2 Roll systems.
After evaluating various options, Jetron integrated Global Graphics Software’s Harlequin Core™ technology. The results were impressive: significantly improved print quality, increased productivity, and enhanced versatility. The integration has given Jetron the opportunity to explore new markets and boost sales, positioning them at the forefront of the industry.
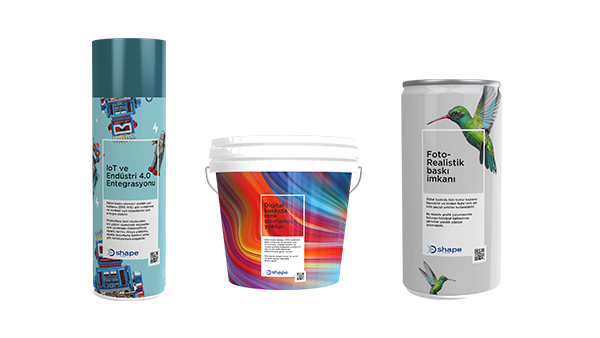
“The implementation of Harlequin Core has proven to be pivotal, offering full integration capabilities with our system. This strategic integration ensures a cohesive and efficient workflow, allowing us to navigate the complexities of digital printing seamlessly.”
Alper Yicek, CTO, Jetron Digital Printing Systems
Further reading:
Be the first to receive our blog posts, news updates and product news. Why not subscribe to our monthly newsletter? Subscribe here