We’ve just added the Harlequin RIP® to the list of products certified as compliant with the Ghent Workgroup’s Output Suite 5 at https://www.gwg.org/ghent-pdf-output-suite-5-compliancy/
It was an interesting exercise, not because it was difficult, but because we started with a bit of archaeology. Back in February 2003 we published an “Application Data Sheet” of instructions for configuring versions 5.3 and 5.5 of the Harlequin RIP to render PDF/X-1a files. We followed that up with another edition for Harlequin 6 (the Eclipse release), addressing PDF/X-3 as well in 2004, and then for Harlequin 7 (Genesis) in 2005.
After that it seemed that PDF/X was sufficiently well understood and so widely adopted in the marketplace that we didn’t need to continue the series. Added to that, we’d added the ability for Harlequin RIPs to recognize PDF/X files and automatically change the RIP configuration around things like overprinting to, as we phrased it at the time, “Do the Right Thing™”.
So when we started writing up how to configure Harlequin for the GWG Output Suite we simply opened up the 2005 doc and replaced the screen grab of the user interface in Harlequin MultiRIP with a one from Harlequin 12.1. In 14 years we’ve added a few options, and, of course, a Windows 10 dialog looks a bit different to one from Windows XP!
We did have to add a couple of extra bullet points to the instructions, especially around perfecting the color management of spots being emulated in process colorants. Some of our color focus over the last decade has been on outputting to a fixed ink set, whether that’s on a digital press or for flexo or offset. So we made the point by delivering our sample output to be reviewed by the GWG as a CMYK raster file … and yes, all of the spot colors in the test suite showed up correctly in their emulations, it all passed 100%.
But that was it.
We thought about adding an indication of which RIP versions the instructions applied to, but ended up simply pointing out when a configuration item had been changed from a check-box to a three-way drop-down menu. The instructions will give you good output from all Harlequin RIPs shipped by Global Graphics in the last decade, and into the future as well.
I love it when stuff just works, and continues to just work, like this. There’s definitely a benefit to aiming to Do the Right Thing™!
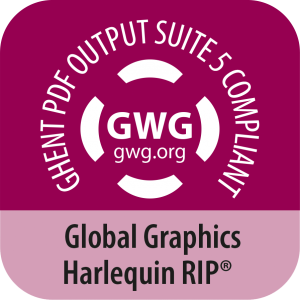
To be the first to receive our blog posts, news updates and product news why not subscribe to our monthly newsletter? Subscribe here