There’s been a lot of emphasis in the industry recently on perceived resolution. I’m sure you will have come across the phrase from major vendors:
“The Xerox Rialto 900 (…) offers 1,000 dpi perceived resolution for high quality output.”
Oce Vaior Print i300: “The multilevel dot modulation in combination with 600x600dpi resolution boosts the print quality of image elements and shadings to perceived 1200 dpi.”
But what is resolution anyway, and is it the only thing we need to worry about to ensure high quality output?
How we perceive resolution has changed over the years. For conventional print and first generation digital presses (except for wide format), resolution was two dimensional (across and along the media). More recently, inkjet presses (and some toner) can place different amounts of colorant at each location on the substrate, using greyscale heads, multiple passes with the same head, or multiple heads imaging at the same location. This means that resolution has effectively become 3D: not only along and across the media, but also in the amount of colorant applied at any single pixel position.
At Global Graphics we call this “multi-level output”, compared to the “binary” output where each pixel can either be coloured or not, with no intermediate steps.
Resolution? Or addressability and droplet size?
As print geeks know well, press resolution has very little to do with resolving power, it is really a marketing simplification to use the word ‘resolution’ for ‘addressability’ – eg at 600 dpi, each addressable pixel is 1/600” from its neighbours. The detail that can be displayed is a factor of droplet size as well as addressability; as droplets get bigger each one covers more than just a single (square!) pixel on the media, so less fine detail is retained.
Droplet placement accuracy also comes into play. In a perfect world we would have a regular grid of droplets, but in practice we don’t usually get one. The variation in separation between droplets can lead to coalescing, mottling or streaking on some substrates, especially on UV inkjet presses, but it can occur on aqueous as well.
Addressability and droplet size affect the rendering of small type and other high-contrast fine detail. Droplet placement accuracy affects texture of final print. So we still don’t have a clear metric for “perceived resolution” …
What about resolution and bit depth?
Using multi-level output can produce smoother rendering of images and other graphics with gradual tone or colour changes than binary output at the same resolution can achieve.
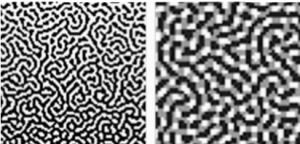
But nozzle redundancy is also vital: In a single pass press, with a page-wide array, a single blocked nozzle will leave a white line down the substrate unless something is built in to fix that, such as nozzle redundancy. And that redundancy must use up some of the press’ capability to use multiple nozzles in the same location for multi-level output, so 1200 dpi nozzles often doesn’t mean 1200 dpi addressability on the substrate.
And sometimes each nozzle can only deliver one droplet size; sometimes it can deliver a variety of sizes.
So what’s the real quality that these presses are capable of? We need a lot of information to really understand what’s going on: dpi across and along the media, number of nozzles imaging any single pixel, droplet sizes available from that nozzle, proportion of nozzles used for redundancy … I don’t think I’ve ever seen a press vendor’s public specification that gives us all the information we want.
Can we even say, simplistically, that higher resolution and bit depth are good? If everything else is equal then yes, in many cases, except that you can push either too far. On an aqueous inkjet, higher resolutions really need smaller highlight droplets; smaller lone droplets tend to disappear into some media and can lead to loss of extreme highlights on the output. Interestingly you end up with output that looks remarkably close to the way flexo loses those same highlights!
And you also need to remember that higher addressability means high computational requirements, and more computations mean more expensive DFEs, higher running costs, maybe even less green … (a faster RIP can offset this, of course!) It also makes the press more expensive, and harder to run as fast.
And what’s the impact on quality?
There are other factors other than bit depth, addressability and droplet size and placement which affect the final result, for example:
- Items affecting ink spread or movement on the substrate such as paper smoothness, absorbency, coatings, ink viscosity and surface tension;
- Movement of the colorant into the substrate, reducing the capability of showing very small detail or saturated colours.
- Registration
- Halftone screening
- Colour management, including ink limitation and reduction
So the ‘virtual’, mathematical discussion of resolution and droplet size are is certainly not the only factor in determining the quality of output. Quality arises from a complex mix of heads, electronics, wave forms, inks, media, resolution, registration, bit depth and half-toning etc. We don’t have a good way to provide a single, understandable quality metric to sum it all up. ISO DTS 15311-1 is defining testing and reporting methodologies in this area, although it still doesn’t provide a simple quality metric.
So what’s the answer?
We just don’t have a single number that sums up the quality capability of a digital press at the moment. But then simply reporting ‘resolution’ has never really fulfilled that role in the past for binary systems, from imagesetters to platesetters to office printers … to digital cameras. So perhaps we shouldn’t be too disappointed.
What should you do when a vendor reports “perceived resolution”? I’d suggest that you take it as an indication of the level in the marketplace that the vendor is intending to address … and then draw your own conclusions based on print samples.
If you’re looking to buy a press, have the vendor:
- Print samples on the media and at the speed that you expect to use
- Use a variety of graphical constructs to explore press behaviour:
- Flat tints at a range of tones and colours
- Smooth graduations, including some long ones all the way to white
- Photographic images, including high and low key, soft-focus and sharp detail
- Fine vector detail such as small serif and sans serif text
If you’re already running a press do the same. Each technology has different strengths and weaknesses; you may even need multiple presses to address all work in your particular target sector. The key thing is to understand what your presses are good at, and what to avoid, and then to work with your customers to achieve the best possible result … and to set expectations appropriately in advance.
If you’re a press vendor, talk to us about how Global Graphics’ multi-level screening technologies can maximise the quality and the value of your hardware.
Read about our latest advances in screening, presented at the Inkjet Conference, October 2015.